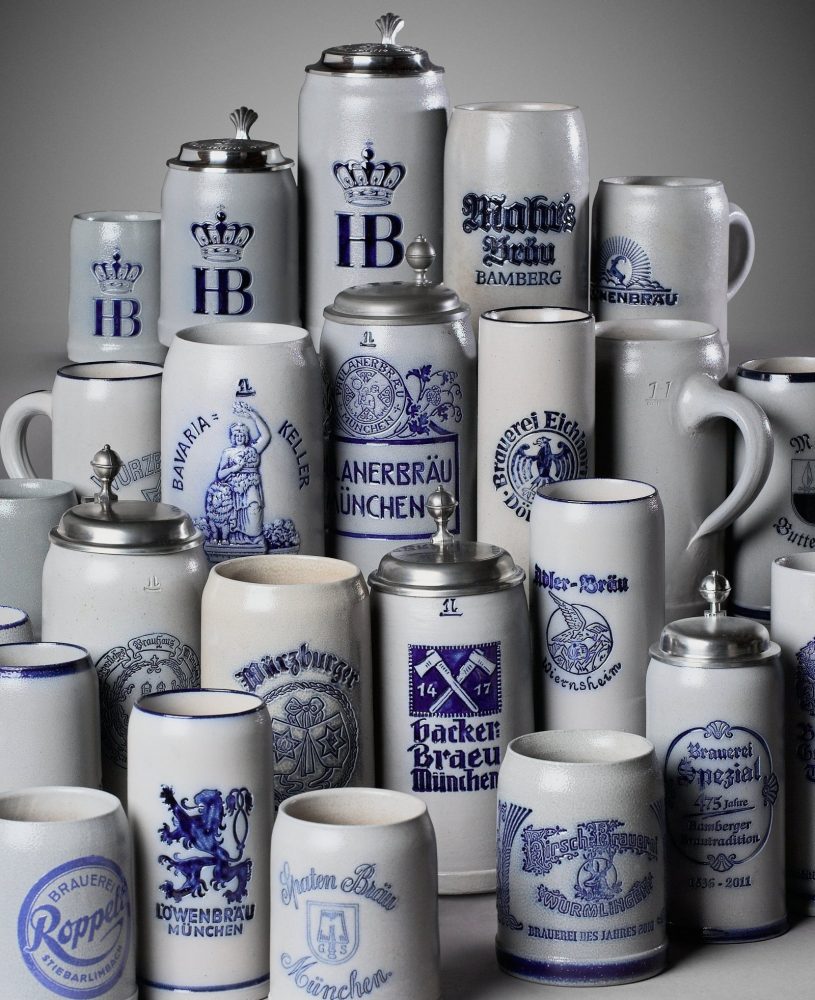
Die Bierkrugmanufaktur
Das wohl traditionsreichste Trinkgefäß für gute Biere ist weit mehr als ein dekoratives Accessoire. Ein salzglasierter Bierkrug vereint die Funktionalität der Keramik mit dem kulturellen Flair beim Biergenuss.
Die aus Steinzeug hergestellten Bierkrüge sorgen dafür, dass eine optimale Trinktemperatur möglichst lange beibehalten wird. So bleibt das Bier auch an warmen Sommertagen angenehm kühl und frisch. Die fein strukturierte Oberfläche der Salzglasur verbessert dabei die Langlebigkeit der Schaumkrone und schützt die Keramik vor chemischen und mechanischen Belastungen. In der Bierkrugmanufaktur der Firma Schilz wird an den handwerklich hergestellten Bierkrug der höchste Qualitätsanspruch gestellt. Brauereien und Gaststätten können dadurch die Werbefläche ihrer individuellen Steinzeugkrüge optimal nutzen.
Die Bembelschmiede
Wer auf der Suche nach dem richtigen Gefäß für guten Ebbelwoi ist, wird an dem salzlgasierten Bembel kaum vorbeikommen – ein Fall für die Bembelschmiede
Der über die Grenzen der hessichen Region hinaus bekannte Bembel ist in der Apfelwein-Szene schon viele Jahre ein fester Bestandteil der Gastronomie. Er dient in der Kombination mit Bechern oder Gläsern als Ausschankgefäß in allen guten Ebbelwoi-Gaststätten. In der Steinzeugmanufaktur der Firma Schilz werden daher Bembel in unterschiedlichsten Varianten gefertigt.
Die Form der Bembel hat einen sowohl kulturellen, als auch funktionalen Hintergrund. Trotz des oft großen Fassungsvermögens ist ein problemloser Ausschank möglich. Das dickwandige Steinzeuggefäß speichert die Temperatur des Apfelweins und vermindert das Aufheizen von Getränken durch warme Gaststättentemperaturen oder Sonnenlicht.
Die hochwertigen Bembel von Schilz sind handwerklich hergestellte Qualitätsprodukte. Unterschiedliche Herstellungsverfahren erlauben uns, abhängig von der Stückzahl und dem Design, unseren Kunden individuelle Bembel mit dem passenden Preis-Leistungsverhältnis fertigen zu können.
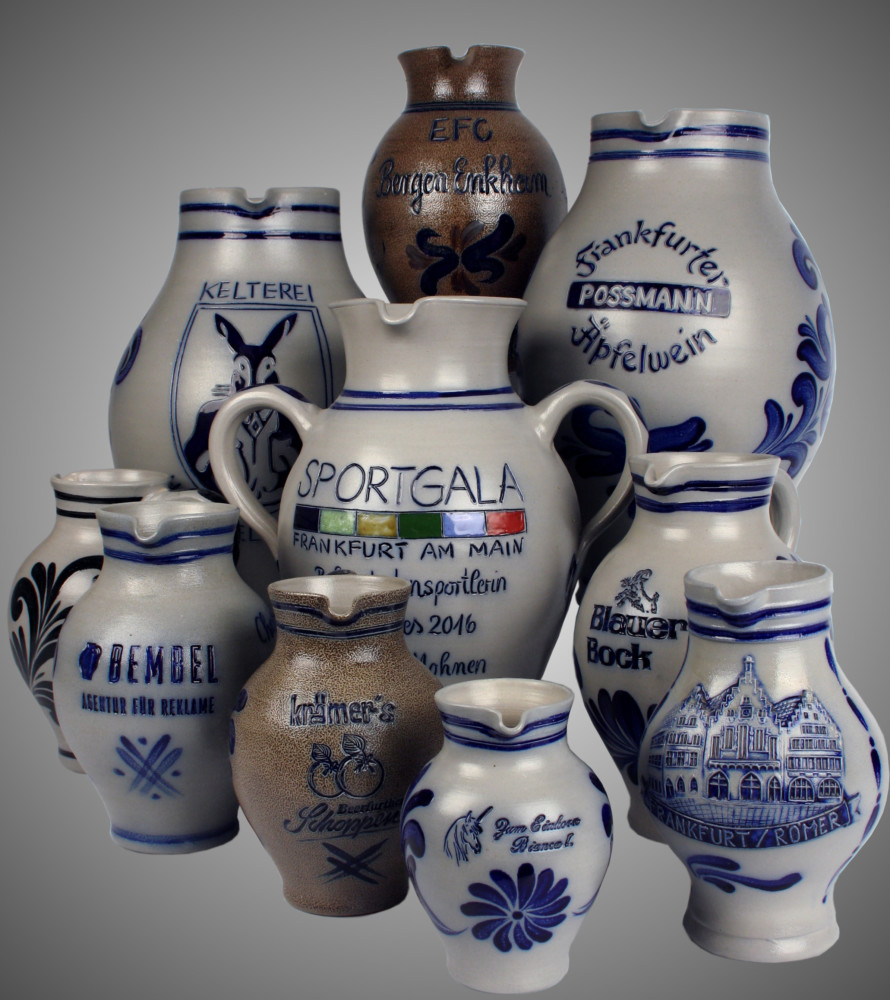
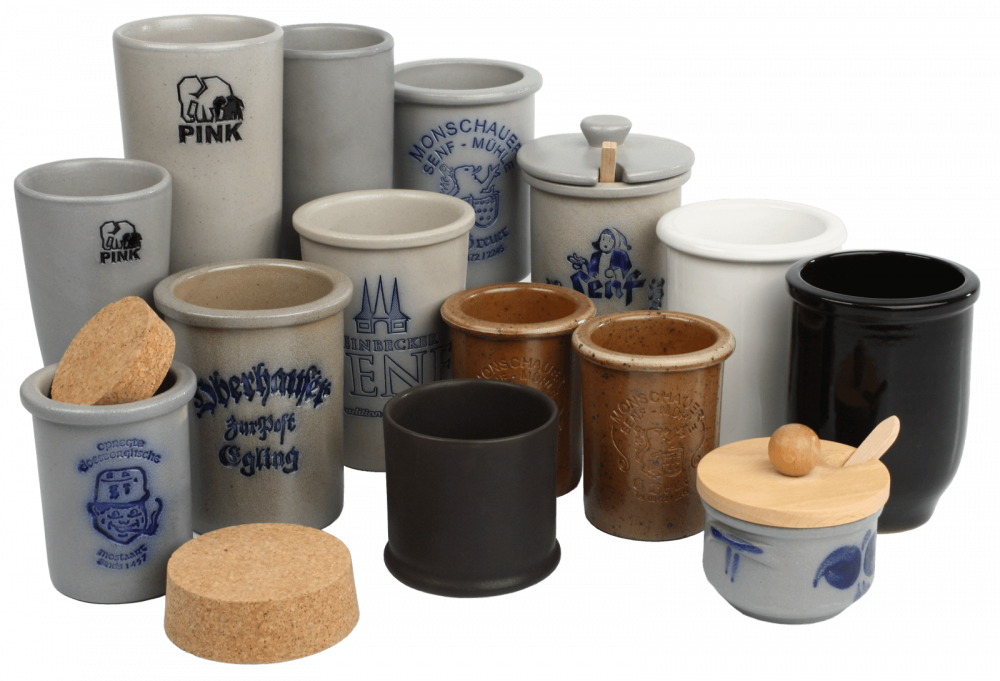
Senftöpfe, Gewürzdosen und Vorratsbehälter
Produkte von besonders hoher Qualität erkennt man oftmals schon an der Verpackung. Die Abgrenzung zu Billigprodukten ist eine der wichtigsten Aufgaben für den Verkauf von hochwertigen Lebensmitteln. Neben den für den Kunden optisch ansprechenenden Merkmalen steigert die Verpackung von Senf in Keramik die Haltbarkeit der Aromen.
Senfverpackungen aus Aluminium oder Kunststoff haben gewiss ihre Vorteile. Sie sind auf die Bedürfnisse der breiten Masse ausgelegt. Soll jedoch ein Produkt durch seine besondere Qualität die Aufmerksamkeit der Menschen erreichen, ist eine dafür geeignete Verpackung der erste Schritt in die richtige Richtung. Handwerklich aus natürlichen Rohstoffen hergestellt, wiederverwendbar und umweltfreundlich in Herstellung und Entsorgung sind unsere Produkte für nachhaltige Konzepte bestens geeignet.